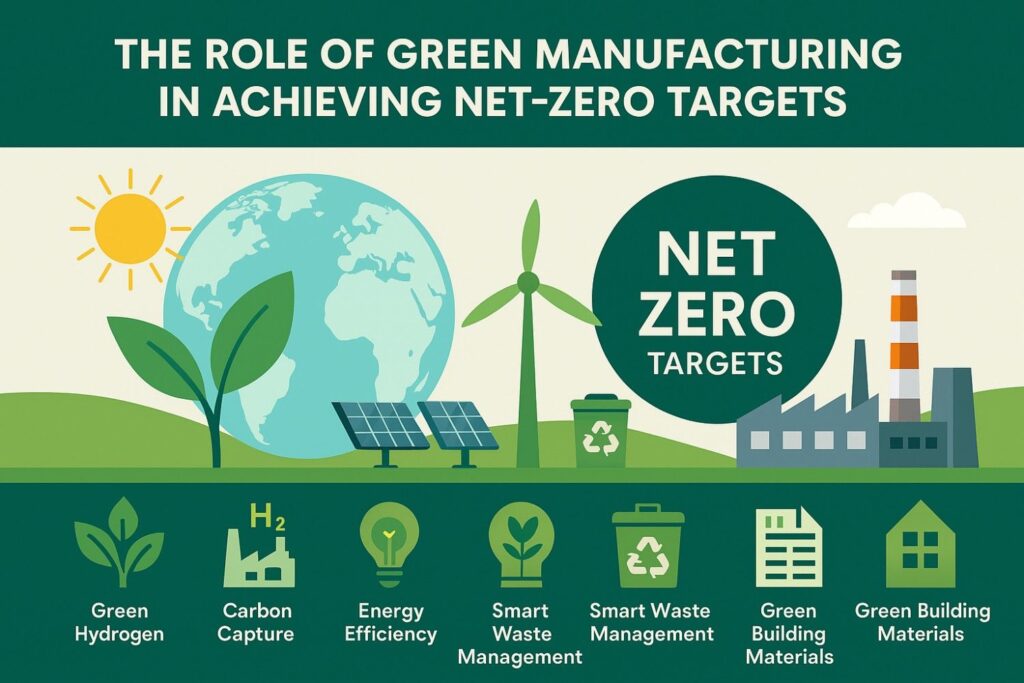
India, the world’s third-largest emitter of greenhouse gases, has committed to achieving net-zero emissions by 2070. As industrial sectors account for over 30% of national emissions, green manufacturing is no longer a future ambition but a strategic necessity. According to EY, India emitted 4.13 gigatons of CO2 equivalent in 2024, with heavy industries like steel, cement, oil and gas, and power being major contributors.
Green manufacturing represents a transformative approach to industrial development, enabling decarbonization while ensuring economic growth. From green hydrogen adoption to carbon capture and energy-efficient systems, eco-conscious innovation is redefining the manufacturing playbook.
What is Green Manufacturing?
Green manufacturing refers to the integration of environmentally sustainable practices into manufacturing processes. It involves the use of energy-efficient systems, renewable energy, waste minimization, and sustainable materials to reduce environmental impact throughout the production cycle.
The goal of green manufacturing is to optimize resource usage while minimizing emissions, pollutants, and ecological disruption. Unlike traditional manufacturing, green manufacturing aligns economic growth with climate goals by embedding sustainability into product design, operations, and supply chains.
How Green Manufacturing Helps Achieve Net-Zero Targets
Green manufacturing enables industries to transition from carbon-intensive operations to more sustainable practices that directly support national and global climate targets. By reducing dependence on fossil fuels, utilizing renewable energy, and implementing energy efficiency improvements, manufacturing companies can significantly lower their greenhouse gas emissions.
Technologies like CCUS and green hydrogen integration provide pathways to manage residual emissions while aligning with global net-zero ambitions. As industrial processes become cleaner and more optimized, green manufacturing serves as a critical pillar in achieving long-term climate resilience.
Green Manufacturing Technology: Innovations and Benefits
Recent advances in green manufacturing technology are enabling industries to implement cleaner, smarter, and more efficient systems. Some notable innovations include:
- Green Hydrogen Technology: Used in steel production and refining to replace carbon-intensive fuels. It reduces emissions at the source and supports hard-to-abate sectors.
- Advanced CCUS Systems: Capture and repurpose CO2 for industrial reuse or long-term storage. These systems offer scalable decarbonization pathways.
- AI-Driven Energy Monitoring: Enables real-time visibility into emissions and consumption, helping optimize energy use and reduce waste.
- Smart Waste Management Systems: Automate waste segregation and recycling, minimizing environmental impact and improving resource efficiency.
- Green Building Materials: Include low-carbon cement, recycled aggregates, and high-performance insulation that reduce embedded emissions in infrastructure.
These technologies improve compliance with environmental standards, reduce operational costs, and enhance competitiveness in a market increasingly focused on sustainable production.
Achieve your net-zero goals with sustainability solutions designed to reduce emissions, optimize resource use, and support long-term environmental compliance. Click here to learn more.
Role of Green Manufacturing Companies in Promoting Sustainability
Green manufacturing companies are playing a leadership role in reshaping industrial sustainability. They not only decarbonize their operations but also influence their entire supply chains. By setting science-based emission reduction targets, investing in renewable energy, and fostering supplier responsibility through green procurement, they create ripple effects across ecosystems. These companies also drive transparency through ESG reporting and integrate sustainability into core business strategy, becoming models of industrial transformation in a low-carbon economy.
The Integration of Green Manufacturing in Operations Management
To unlock the full potential of green manufacturing, it must be integrated into the core of operations management. This involves:
- Redesigning production lines to minimize waste and energy usage. Energy audits and lean manufacturing practices are key tools.
- Embedding sustainability metrics into daily operations and team KPIs, making it a performance standard rather than a side initiative.
- Upskilling the workforce in sustainable practices and energy management, building a culture of continuous improvement.
- Using digital twins and simulation tools to test changes in real-time and guide more sustainable decision-making at scale.
Eco-Friendly Manufacturers: Leading the Way Toward Sustainability
Eco-friendly manufacturers take a proactive stance in addressing environmental challenges through innovation and accountability. Their strategies often include closed-loop systems, sustainable packaging solutions, water conservation initiatives, and low-impact logistics.
These manufacturers lead by example, setting higher environmental benchmarks within their industries. As sustainability becomes a core differentiator, these organizations are increasingly recognized as trusted, future-ready partners by customers, investors, and regulatory bodies.
Green Manufacturing in Gas Plant Engineering Services
In the energy sector, gas plant engineering is undergoing a green transformation. From optimizing thermal efficiency to integrating renewable energy inputs, sustainable design is reshaping traditional engineering practices. Green manufacturing principles are being applied to:
- Retrofit aging infrastructure with energy-efficient systems
- Adopt low-emission turbine and compressor technologies
- Utilize green hydrogen in combustion processes
- Monitor and reduce fugitive methane emissions
These advancements reduce operational emissions and improve long-term compliance for gas plant operations.
Benefits of Green Manufacturing in Gas Plant Engineering
Implementing green manufacturing in gas plant engineering offers several advantages:
- Lower Emissions: Reduces CO2 and methane outputs at source, helping meet emission caps.
- Improved Energy Efficiency: Enhances system performance and minimizes resource waste.
- Enhanced Equipment Life: Cleaner operations reduce wear and extend component durability.
- Regulatory Compliance: Helps meet tightening environmental norms and reporting obligations.
- Cost Savings: Optimized systems translate into lower energy use and maintenance costs over time.
Future Trends in Green Manufacturing and Sustainability
Looking ahead, green manufacturing will continue evolving with innovation and policy alignment. Key trends include:
- Growth of Green Hydrogen Economy: Expected to become a mainstream fuel for power, industry, and transport.
- Decentralized Energy Systems: On-site solar, storage, and microgrids will improve resilience and reduce reliance on carbon-based grids.
- AI-Powered Process Optimization: Drives smarter decision-making by analyzing vast amounts of operational and environmental data.
- Sustainable Product Design: Tools like life-cycle analysis will guide the creation of low-impact, recyclable products.
- Green Finance Integration: More industries will access capital through sustainability-linked loans and ESG investments.
Conclusion
Green manufacturing is at the heart of the world’s transition to net zero. Through innovation, operational integration, and a deep commitment to sustainability, industries can decouple growth from environmental degradation. While challenges remain, the transition toward net-zero emissions represents a pivotal transformation in the energy sector—signaling a more responsible and resilient industrial future.
Ingenero helps organizations take measurable steps toward net zero through tailored sustainability solutions, carbon mitigation strategies, and process optimization. With extensive domain expertise, Ingenero bridges engineering and environmental priorities, delivering practical pathways to long-term climate goals.
By aligning technology, policy, and purpose, green manufacturing is not just a means to an end but the foundation of future-ready, sustainable industrial ecosystems.
FAQs
Green manufacturing technologies include systems and tools that minimize environmental impact during production. These range from renewable energy integration and carbon capture to smart waste management, AI-driven monitoring, and the use of sustainable raw materials and cleaner fuels.
Yes, green manufacturing can lower costs over time by improving energy efficiency, reducing material waste, and minimizing regulatory penalties. Optimized resource use and predictive maintenance also contribute to long-term operational savings for manufacturers across sectors.
Green manufacturing companies lead by embedding sustainability into their operations, supply chains, and product design. They invest in clean technologies, practice ESG reporting, and influence industry standards by aligning with science-based targets and global climate frameworks.